Another day, a new lease on breathing, and progress!
Felt good this morning, the air goes in and out, the blood goes round and round, with very few exceptions. Im finally feeling up to medium sized tasks, and the doc says just to not get nuts, so Im back at it.
Filleting was the plan of the day. Fillet the inside of the hull today, tape tomorrow, glass friday. Should be a good schedule, not too much to ask.
Filleting went well. There really are relatively few places that need a big (13mm or 1/2" radius) fillet laid in, so this was cake. Nice mixing Marinepoxy from www.boatbuildercentral.com really did the trick.
I didn't think about taking pics until after the filleting was done. Ironically, it was done at about 11:30 this morning! I hadn't anticipated it going so smoothly or quickly, so I was enthused. A whole afternoon left....
Out came the prevously cut tape. Started rolling everything out, checking fit here and there. Hell, why not, I bet I can get this taped today too! I threw one layer out, then remembered that I do have a camera, and a blog that occasionally gets read by moderately interested people.
The transom fillets:
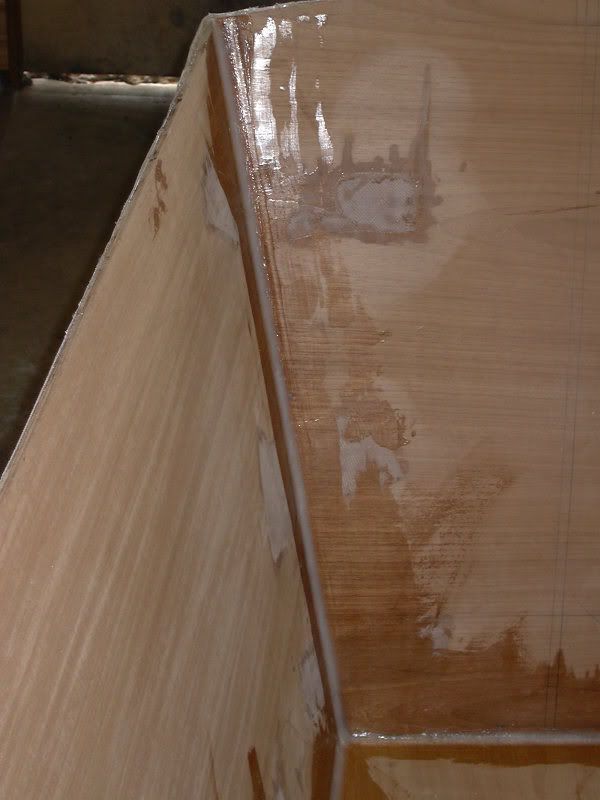
The bow fillet (note how it tapers to nothing as the bow gains its fullness):
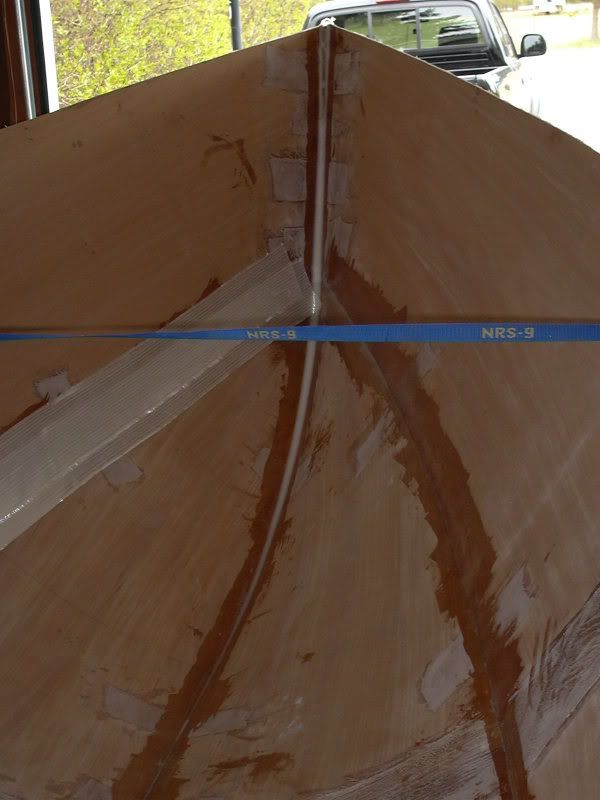
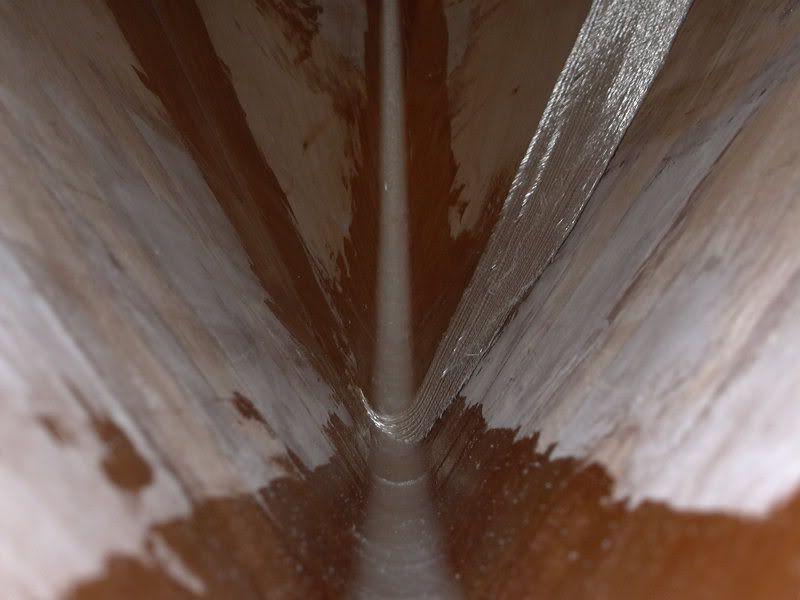
Then began taping in earnest. The fillets were still quite tacky, but not wet anymore. This (if you are doing a similar project) is a convenient fact to keep in mind. I could immediately lay my tape out, even in the 2 and 3 layer fashion required, and stick it in place loosely until I got the saturating epoxy on it. EXTREMELY helpful part of working "wet on wet" as they say. Saved me at least an hour or two of prep work, and a couple hours of sanding time.
Picked up the camera during a glove change:
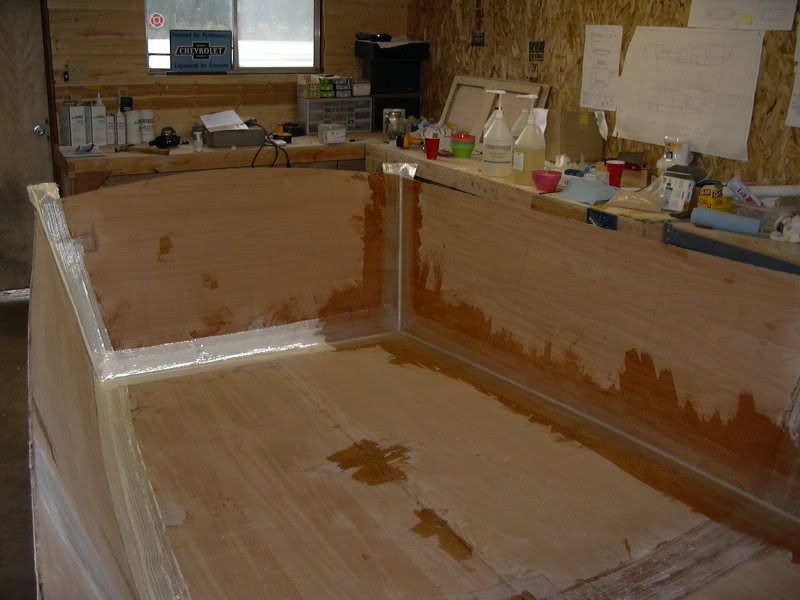
When I finished all my tidying up and cleaning off of the supplies, I then degloved to shoot pictures of my handiwork. This is partly for your informative pleasure and mostly for my inflating ego.
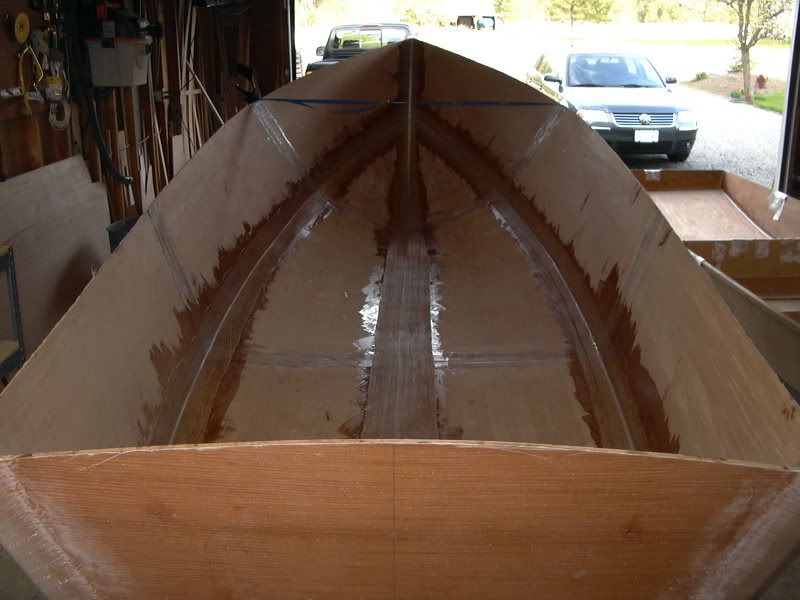
The weave a little closer:
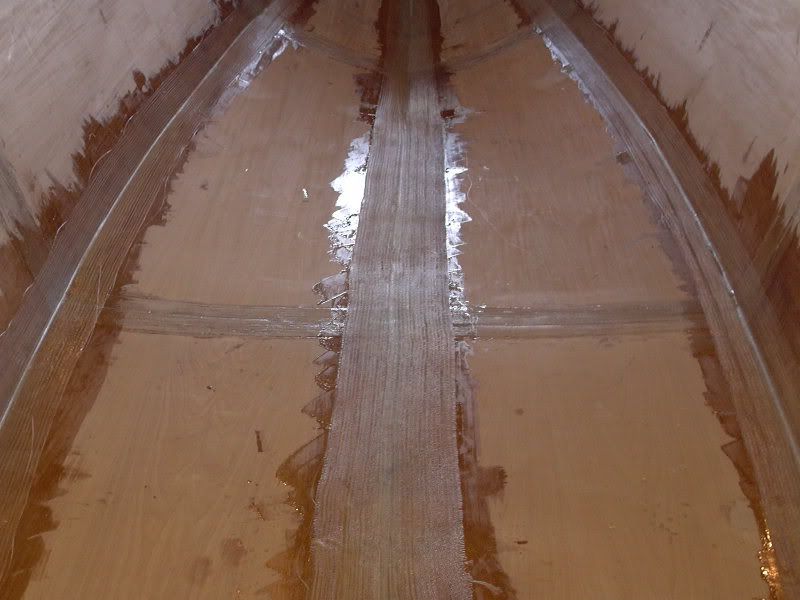
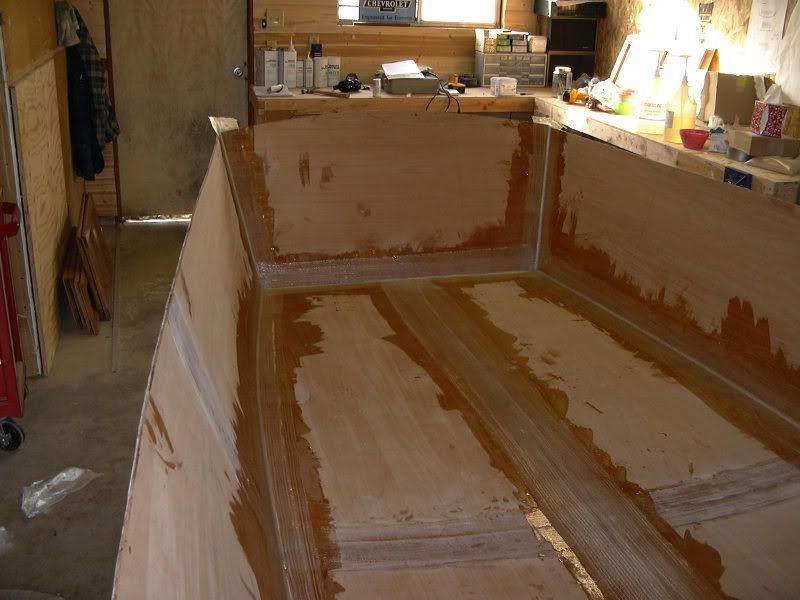
Shot down the bow to show the fillet covered with glass:
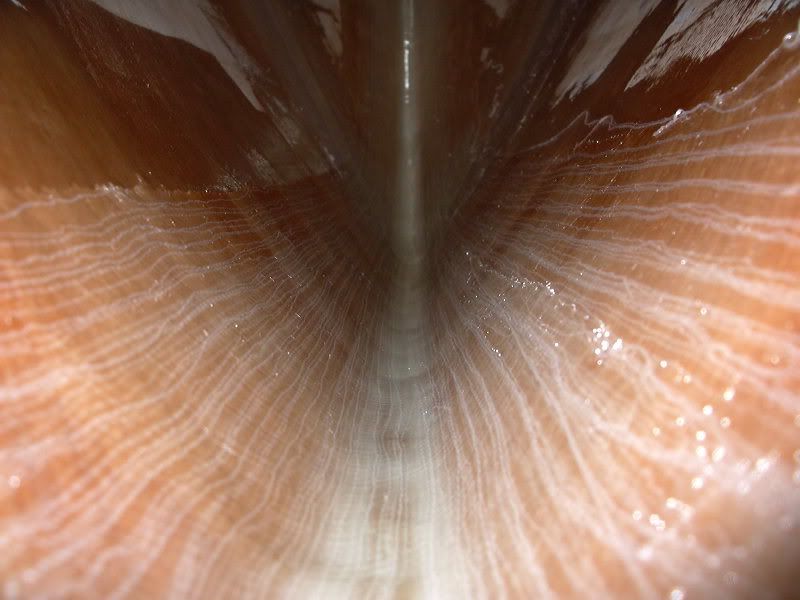
For the fortuitous part:
I had set out on my plan for fiberglassing happening friday. I then posted a few questions over at http://forums.bateau2.com/ concerning the interior fiberglassing. On certain designs you can use the remnants to sheath the inside in strips. Unfortunately for me, I would have to make too many little strips and odds and ends, so I chose to order up another roll of 20 yds. This is a whopping $175 or so, and in the grand scheme of the boat a mere drop in the bucket. Plus I will use the extra to build other projects in the future (that boylesboats jonboat Ive been lazing around thinking about). I asked the guys over at e-boat (from whence the plans and all supplies came) if they could get the rolls to me by friday, to which they said no prob. My order was taken, processed, and dropped at DHL in the course of 3 hrs. I got my first shipping notice from DHL an hour later, saying my goodies should be here thurs. PERFECT! Huge help, amazing service and a good crew.
Flash to today. Lo and behold DHL pops in a full day early with my glass! I will be cutting, prepping, and laying glass tomorrow......
Jacques, Joel, Dave, Thanks!
E