5 weeks people, 5 weeks. First the shipment missed the truck, then got on the next truck but was hung up because that truck wasn't full for 2 weeks. Then to add insult to injury, a load of flooring couldn't pass customs. Another week on the loading dock. Finally, it trickled into the store, and I happened to get there BEFORE they unloaded it. I helped the stockers unload 15 other sheets of ply before we could get down to mine in the stack. Ugh.
In the meanwhile, I had to keep myself occupied:
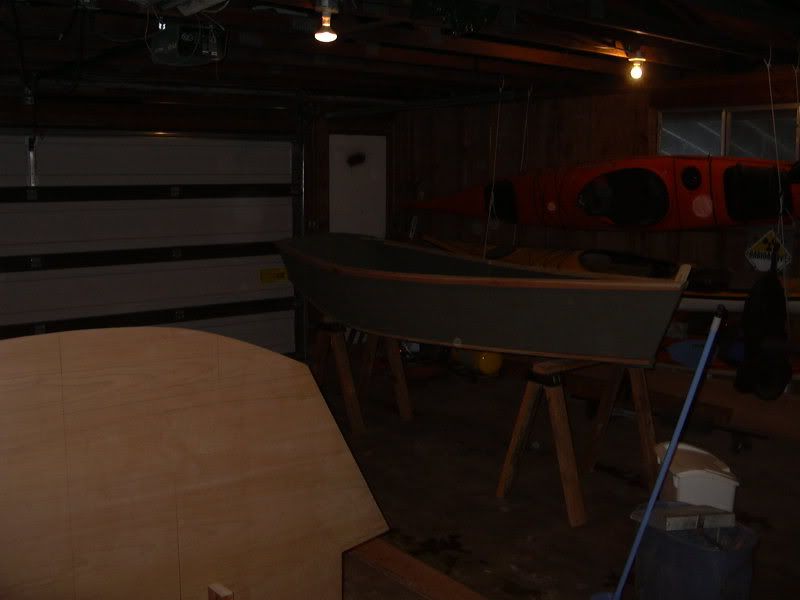
In an earlier post I referred to (and showed a pic of) a Dave Beede designed Summerbreeze. A little scrap ply, some random extra redwood and doug fir laying around (note: redwood sucks for gunnels, both broke, one broke twice) turns into a nice little rowboat. A neighbor gave me some housepaint, which Ive used to prime the panels. Better than a kick in the teeth I s'pose.
On to the star of our show!
Of general importance on this episode, is working with epoxy in an unheated shop. I chose not to heat the shop as it is uninsulated, but to heat the materials to cure the epoxy. 70 degrees is our target, but 40 is the working temp to achieve. Using a 1500 watt quartz electric heater teamed with a pair of 250/500 watt quartz worklights we had a nice random looking assembly which successfully got a solid cure on the epoxy overnight with outside temps in the teens.
The menagerie:
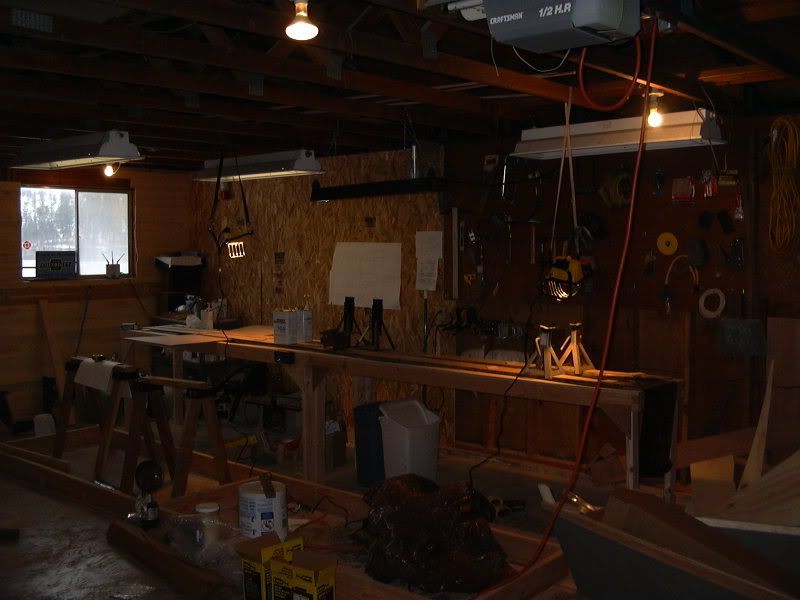
Though strange looking and a half-assed job of hanging everything, it was relatively effective. Relative in that your humble narrator is an idiot and managed to leave both lights on at 250 watts. Eh, yeah, im retarded. There are times that my boatbuilding is more like a college basketball game. Whoever makes fewer mistakes wins, and Im on the losing team.
This is the stringer assembly per plans, and finally in the flesh:
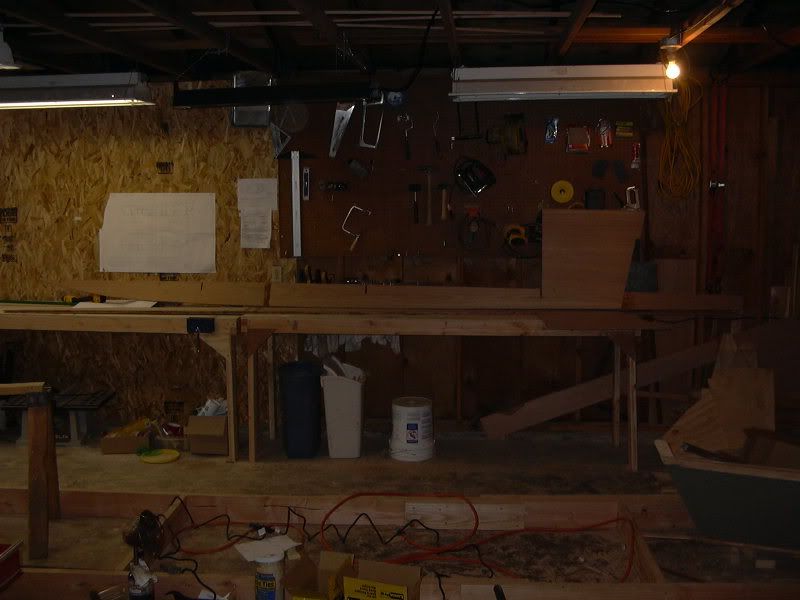
Seeing that after all this time makes me tingly in ways boatbuilding shouldn't. Don't tell my wife. Oh wait, she reads this too. And her brother. Ah well.
The ladder framed strongback is nice and square, moved to the most advantageous place on the relatively small floorspace I have. Then we mix in those bulkheads I cut EEONS ago to start the building jig. I only had time to notch and put up the C frame as well as the E frame which will be the bookends of the main passenger compartment. Add a liberal dose of stringers and we have the makings of a 3 dimensional structure!
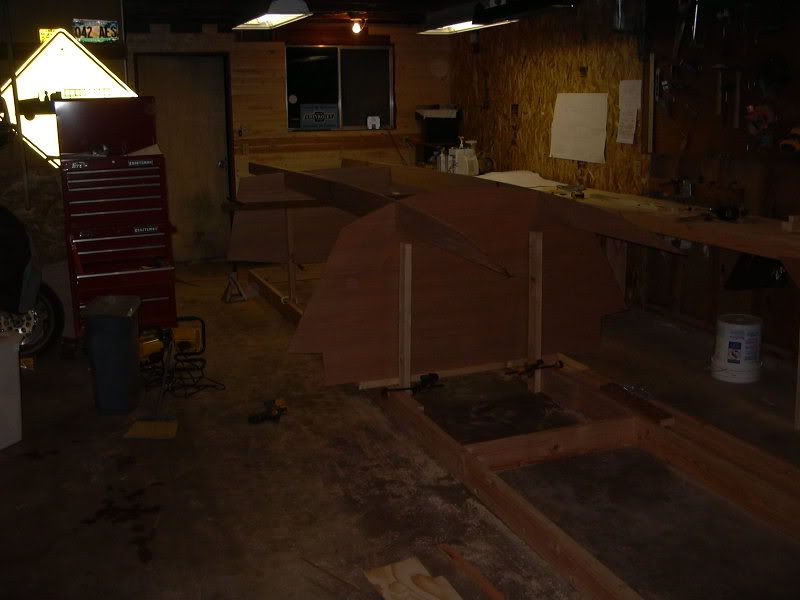
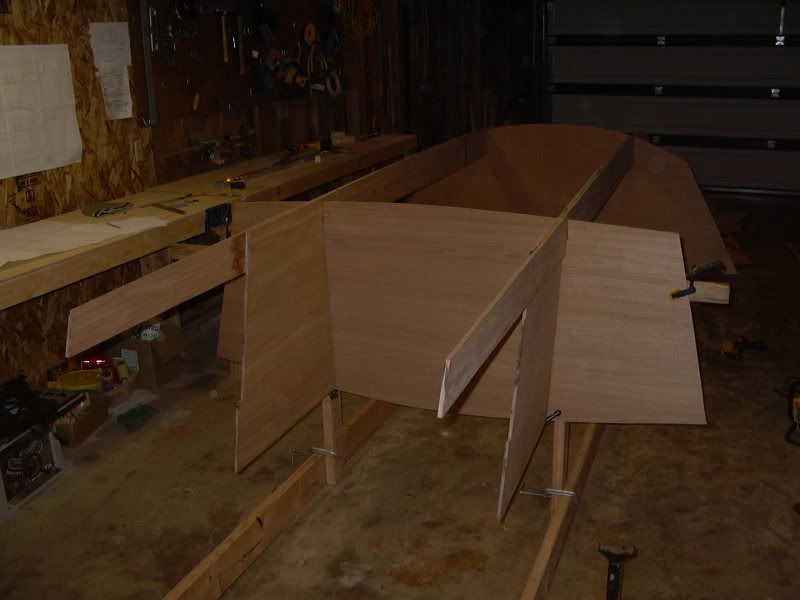
Cmon, get excited! I know I am!
For our next installment, I will try to get the frames up and leveled in, make several mistakes, cost myself some money, screw up at least one cut, throw a tool or two, some strange concoctions of nouns and sware words, and out will pop a completed jig!
Stay tuned. Same boat time, same boat channel.
E